GEMBA
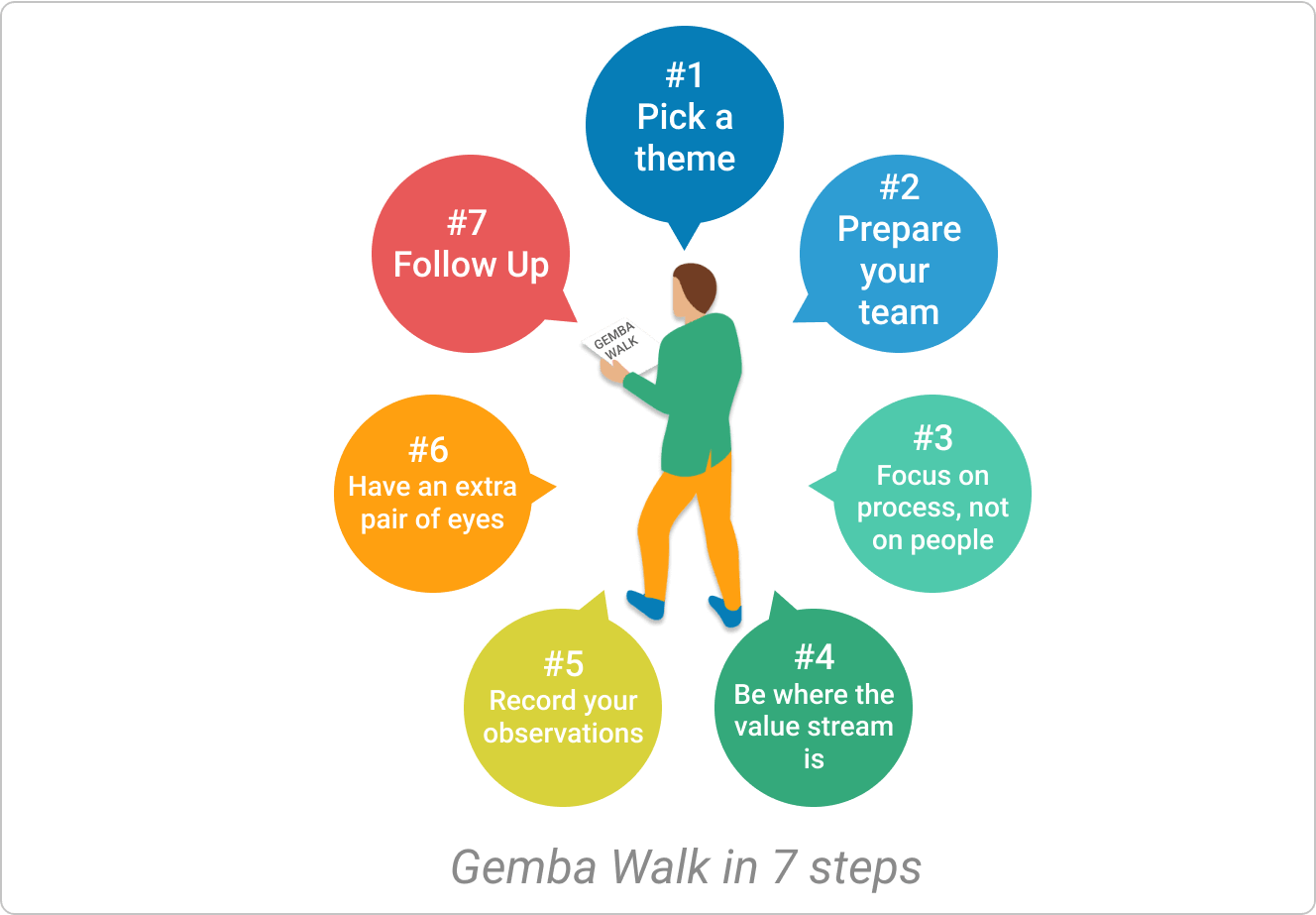
The Gemba walk is an essential part of the Lean Management philosophy. Its initial purpose is to allow managers and leaders to observe the actual work process, engage with employees, gain knowledge about the work process and explore opportunities for continuous improvement.
The term “gemba” comes from Japanese and it means “the real place”. In Lean management, “gemba” is the most important place for a team as it is the place where the real work happens.
There are 3 important elements of this lean manufacturing tool:
1. Go and see. The main idea of the Gemba walk is managers and leaders on every level to take regular walks around the shop floor and to be involved in finding wasteful activities.
2. Ask why. The main objective of a Gemba walk is to explore the value stream in details and locate its problematic parts through active communication. The good leader is always eager to listen rather than talk. Here is why you may use different techniques such as 5W1H Method in order to identify problematic parts of the process.3.
3. Respect the people. Have in mind that a Gemba walk is not a “boss walk”. Pointing fingers and blaming people is exactly what you don’t have to do. You are not there to judge and review results. You are there to collaborate with the team and find problems together. Try to focus on finding the weak spots of the process, not of the people.
7 Steps to Follow When You Go to Gemba
Before you walk the shop floor, you need to make a plan and follow the steps. The plan should depend on your goals and objectives.
1. Pick a theme. When you go to Gemba, you have to choose a theme. This will help you focus all your efforts and be effective. There are different themes you may want explore such as: productivity, cost efficiency, safety and etc. In order to be as much precise as possible, you will also need to prepare a list of question you are going to ask.
2. Prepare your team. The team that will be observed should be prepared for what is going to happen. All team members need to have a clear understanding that the Gemba walk is a common process where the final destination is Continous Improvement PDCA. This way workers will feel much more comfortable and willing to collaborate.
3. Focus on process, not on people. You need to remember that a Gemba walk is not the right time for evaluating the performance of your team. The main purpose is to observe, understand and improve the process. If you focus on people’s personal abilities, you will only face a resistance.
4. Be where the value stream is. Following the value chain will give you the best opportunities to identify areas with a high potential of waste activities. Eliminating those activities will help you improve the overall performance.
5. Record your observations. Don’t make suggestions during the walk. Write down everything that grabs your attention or even record it with your smartphone. In some cases, you will probably be tempted to offer a solution immediately, but this would be wrong. Leave the analysis for later. You will be much more precise after you have all the facts available. Furthermore, the broad overview can offer you opportunities to use effective problem-solving tools such as 5W1H Method Much better than an instant gut feeling.
6. An extra pair of eyes. It may be a good idea to invite a colleague from another department. Someone with totally different daily tasks. People who are less familiar with the processes usually have a fresh point of view and ask different questions that you may never ask.
7. Follow-up. Even if you don’t find anything significant during your Gemba walk, you need to share with the team what you have learned or seen. Otherwise, the team will only have the feeling of being watched. If you are going to take actions after the walk, inform the team about the upcoming changes and why they are necessary.